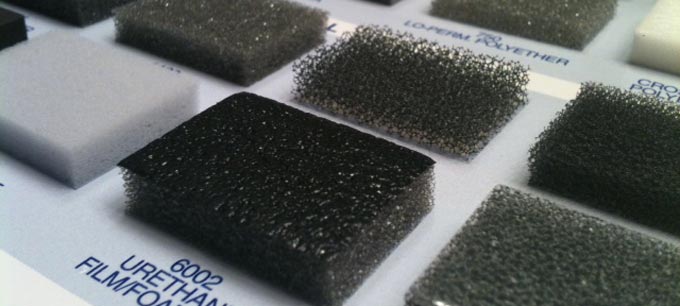
Recently, we had a Minneapolis company come to us needing help choosing a material and cutting process for a new line of foam disks.
By thoroughly learning the specs and end uses, we were able to help the company save time and money while developing a great product.
Specific Foam Characteristics
This customer had their product’s specifications already in mind when they first came to us for help. (If you don’t happen to have a list of product requirements, we’re more than happy to help discover exactly what your product will need to endure).
This foam disk needed to:
- be soft
- be easily compressed
- have an adhesive that endures harsh environmental conditions
- have a good compression set resistance (to create a seal when compressed repeatedly)
Personal Consultations
Our team collaborated with our client’s engineers face-to-face to fully understand the logistics of their design. After gathering all of the critical info, we brought out samples of different material combinations for the customer to choose from.
After they chose a material from the samples, our team went quickly moved to the next step of their order.
Kiss Cutting Foam
To shape the foam disk, we decided to kiss cut the foam on a continuous release liner in roll form (rather than individually die cutting the parts). This allowed our assemblers to peel the parts off quickly because they wouldn’t have to get the release liner started for every part.
Kiss cutting the foam disks saved hours of production time for us, which made the product ready for the customer even sooner.
Taking it one step further, we designed a method to remove the used webbing of material from the kiss cut part rolls. This created less waste for the customer as well as making it even easier and faster for our assemblers to complete their tasks.
Pricing and Completion
By selecting the ideal material combined with this specific manufacturing process, we were able to help our customer get a very competitive price, making this was a win-win for both their company and ours.
Our team always tries to take an extra step to help each customer find the right material and give them an easy, stress-free experience. If you’re looking to manufacture your foam products, give us a call. We’ll help you find the best materials and fabrication processes.