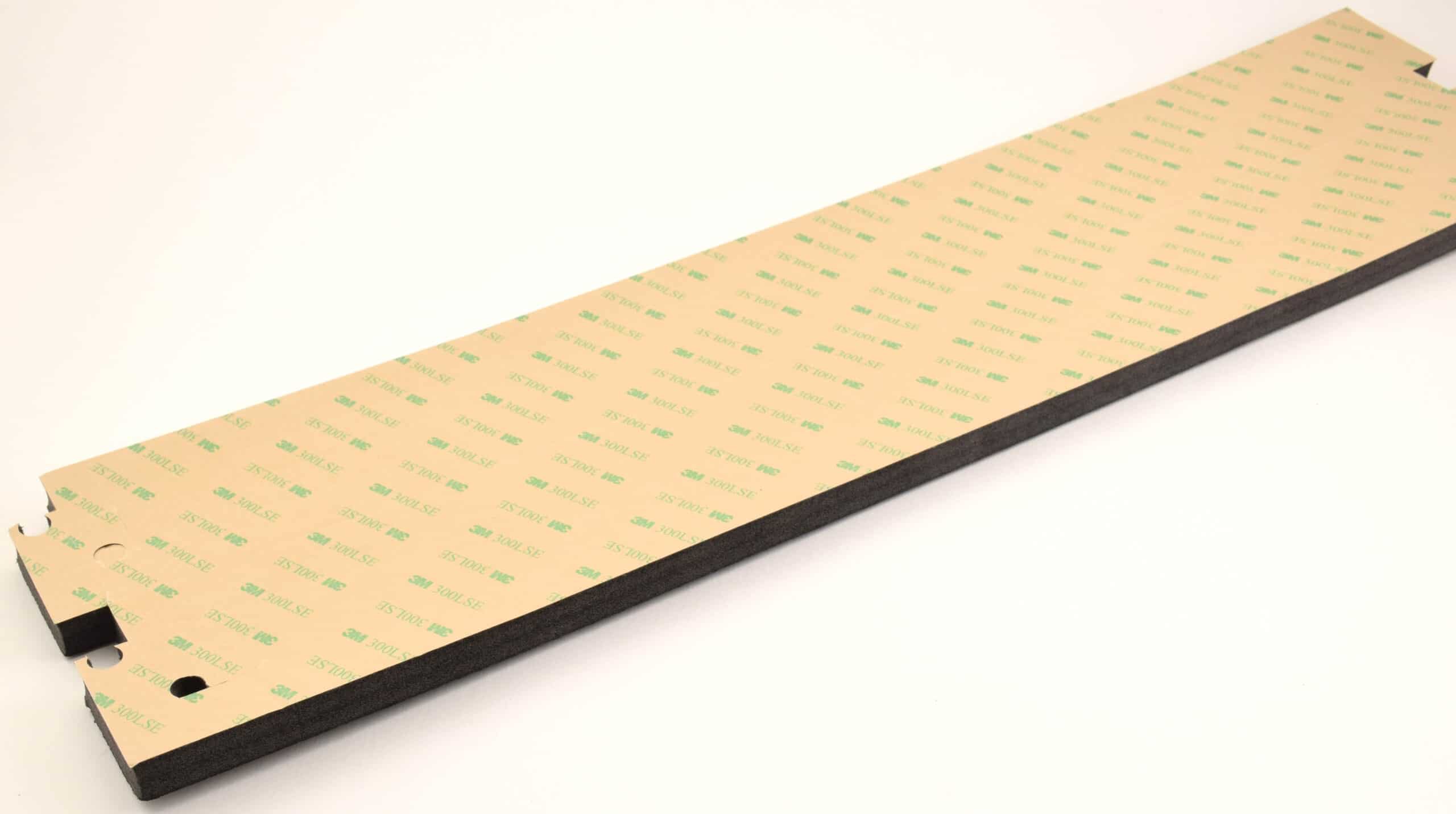
Pressure sensitive adhesives (PSAs) and foam tapes are used to attach to the surfaces of two substrates. When selecting a PSA or tape, not only must you consider surface condition (roughness, smoothness, porosity, cleanliness, flexibility, surface energy) but also the environment (temperature range, chemical resistance, UV light).
There are many different types of PSAs available with a range of physical properties. The most common types of PSAs are rubber, acrylic and silicone.
Rubber Adhesives
Rubber adhesives are normally a low-cost option used for general purpose, short-term, line-to-line applications. They usually have a good initial tack to many different substrates.
Acrylic Adhesives
Acrylic adhesives provide resistance to solvents, UV light, elevated temperatures, plasticizers and chemical reagents. They tend to be more costly than rubber-based varieties but provide better long-term aging and environmental resistance. They have low-to-moderate initial tack and adhesion but typically setup to a full bond within 24 to 48 hours. Acrylic adhesives generally do not adhere well to low-surface-energy substrates.
Silicone Adhesives
Silicone adhesives are predominantly selected for the most demanding industrial applications because of their inherent resistance to temperature extremes, moisture and chemicals. Silicone adhesives also offer excellent dielectric properties so that they are often used as pressure sensitive tapes for the electronics industry.
Silicone PSAs provide premium performance and are, on average, more expensive than all other types of PSAs. The following list shows the variety of products that AFP offers based on the adhesive type:
- Double coated (carrier)
- Electrically conductive
- High surface energy
- Low surface energy
- Optically clear
- Repositionable (high tack or low tack)
- Thermally conductive
- Transfer tape (free film)
- VHB
Every call, question and quote request will be answered by an owner.